- Mot(s) clé(s) :
- Economie circulaire bâtiment
Béton de site : retour aux procédés ancestraux
Le contenu est réservé à nos adhérents. Pour le consulter
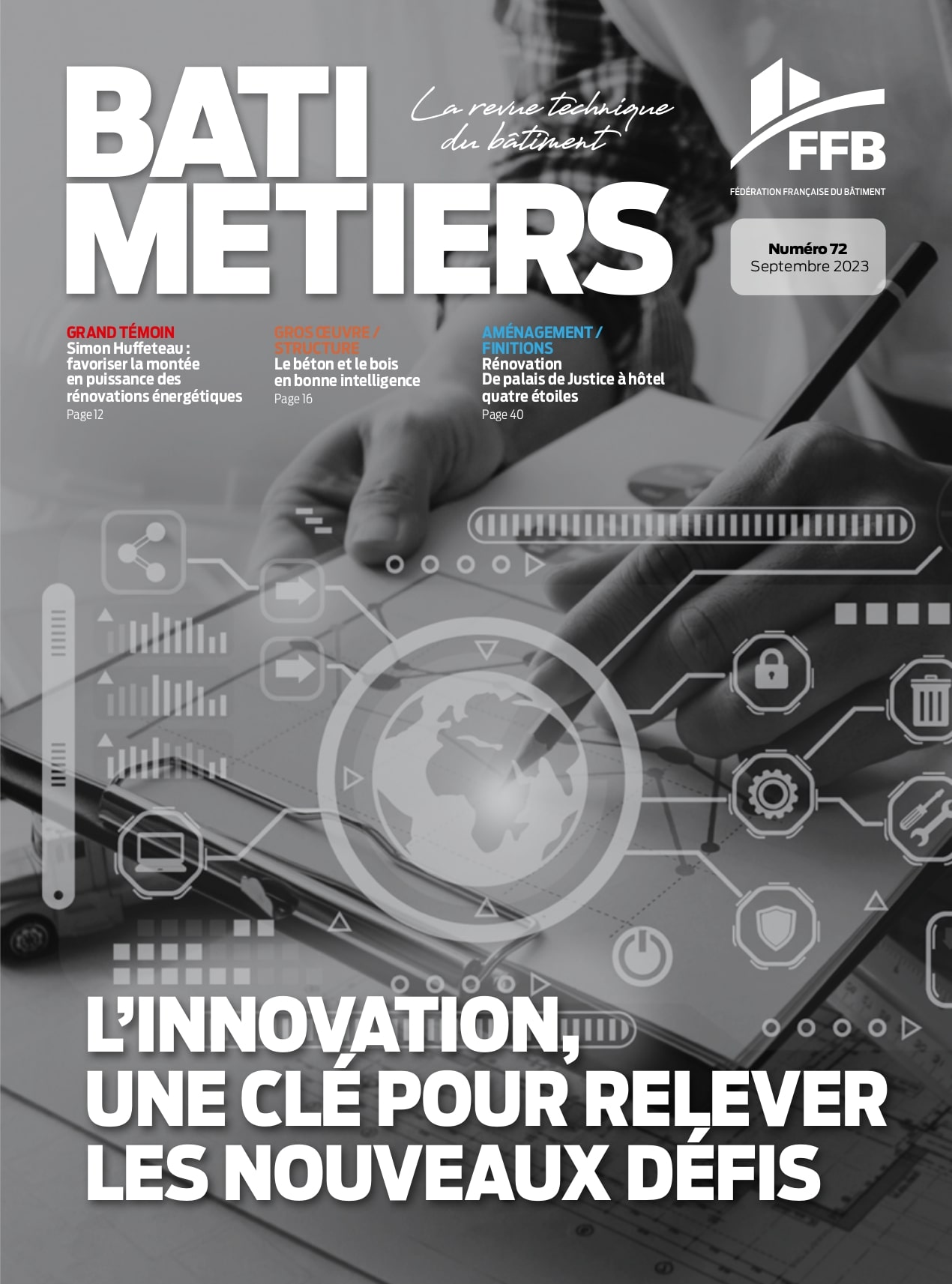
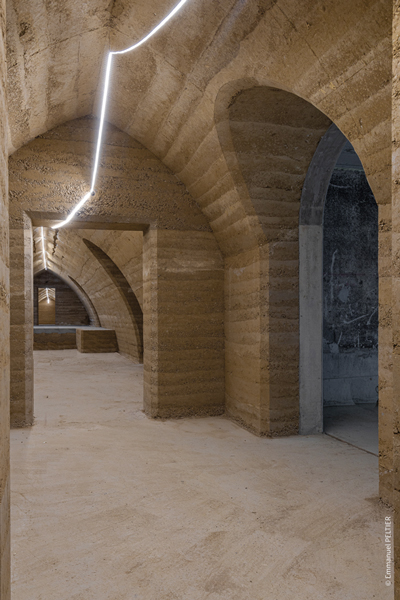
© Emmanuel Peltier
Un cycle vertueux
Longtemps abandonnée au profit de solutions standardisées moins complexes et moins gourmandes en main-d’œuvre, la technique du béton de site revient au goût du jour, y compris sur de grands projets, comme le mur d’enceinte de la citadelle de Bastia.
Ses atouts ? Elle permet de valoriser une ressource locale, abondante et renouvelable ; de travailler en circuit court, avec des transports très limités ; de ne pas produire de déchets : le bâtiment peut être facilement déconstruit et les éléments rendus à la parcelle.
La caractérisation de la terre dès la phase d’étude et la réalisation de la formulation sont deux étapes clés pour assurer sa qualité.
La première étape a consisté à analyser la constitution de la terre, un sable plus ou moins argileux qui a été soigneusement stocké, tamisé et criblé pour ne garder que les matériaux alluvionnaires, réglementés pour confectionner le béton. La quantité de matière étant insuffisante, l’entreprise Fayat, en collaboration avec la maîtrise d’œuvre Batiserf et Studio Méditerranée, a choisi de compléter le terrassement avec des matériaux concassés (béton, briques et parpaings) provenant des bâtiments existants du site. Une démarche pionnière, ce type de matériaux étant habituellement réservé aux sous-couches de voiries ou aux remblais de canalisations.
L’étape d’après, essentielle, a été de réaliser la formulation, opérée dans une centrale à béton à même le site, pour obtenir la résistance requise pour la construction.
Ce qui fait la qualité d’un tel béton sec, qui n’est pas ferraillé, est à la fois la qualité de la formule et le compactage, qui donne de la densité à la matière
Celui-ci a ici été réalisé à la main par couches de 18 cm en utilisant un fouloir pneumatique.
La particularité de la structure finale est d’obtenir des murs de grande épaisseur – de 30 à 50 cm – et une forme en ogives permettant de répartir au mieux les efforts en économisant la matière. Ici, la technique apparaît particulièrement adaptée à son usage de destination, des caves voûtées, qui doivent garder une température et une hygrométrie constantes, été comme hiver. Elle s’inscrit également en cohérence avec le patrimoine existant.
Un point de vigilance toutefois : l’attention portée à la qualité lors de la mise en place. « Tout est réalisé manuellement, ce qui demande du temps et nécessite un contrôle rigoureux de la part du chef de chantier », souligne Francesco Calderan. Des carottages des bétons sont régulièrement prélevés et écrasés afin de vérifier leur résistance, comme le prévoient les procédures qualité de l’entreprise.
Chiffres clés
Le mélange a été réalisé à partir de 950kg de sable argileux et près de 700kg de béton, briques et parpaings issus de bâtiments démolis.
La résistance requise pour la formulation était de 8 mégapascals (MPa), elle atteint de 14 à 16MPa en moyenne.
Contenu réservé aux adhérents FFB
- Profitez aussi de conseils et de soutien
Des services de qualité, de proximité, avec des experts du Bâtiment qui connaissent vos enjeux métier et vous accompagnent dans votre quotidien d'entrepreneur.
- Intégrez un réseau de 50 000 entreprises
La FFB est fière de représenter toutes les entreprises du bâtiment, les 2/3 de nos adhérent(e)s sont des entreprises artisanales.
- Bénéficiez des dernières informations
Recevez Bâtiment actualité 2 fois par mois pour anticiper et formez-vous aux évolutions des métiers ou de la législation.